Most predictive maintenance initiatives that fail do so for reasons that could be proactively addressed in advance. Based on our experience as consultants in the field, we have identified five significant pitfalls commonly encountered by machine manufacturers when implementing predictive maintenance strategies. Throughout this article, we will provide you with a comprehensive understanding of these pitfalls and offer practical guidance to help you avoid them successfully. By steering clear of these common pitfalls, you can ensure the successful implementation of predictive maintenance and stay ahead in a competitive industry.
1. The Perceived Hierarchy of Maintenance Strategies
One common misperception is that predictive maintenance is inherently superior to preventive and reactive maintenance without considering the specific needs of each. To avoid this pitfall, it's crucial to understand that the effectiveness of each strategy depends on the unique characteristics of your machinery and the potential consequences of specific failure modes. Consider an example: While preventive maintenance might be suitable for a critical component like a milling machine’s spindle, reactive maintenance might suffice for easily replaceable wearing parts like the tools. Gain an in-depth understanding of your equipment, align your maintenance strategy with your organizational objectives and your customers’ needs, and employ data-driven insights to design a strategy that maximizes its impact. By tailoring your approach to the specific needs of your machinery and business goals, you can avoid this common misconception.
2. The Business Case Dilemma
Frequently, machine manufacturers embark on predictive maintenance projects without a well-defined business case. To navigate this pitfall successfully, it's imperative to clearly define the purpose and benefits of your predictive maintenance efforts. The lean validation approach, similar to a "build, measure, learn" loop based on lean minimum viable products (MVPs) without heavy upfront investment, should then guide your business case’s validation. This is how you can ensure that your business case not only revolves around the technology but also articulates how it benefits your customers and contributes to your bottom line. In the following figure will give you a first understanding of business cases enabled by predictive maintenance.
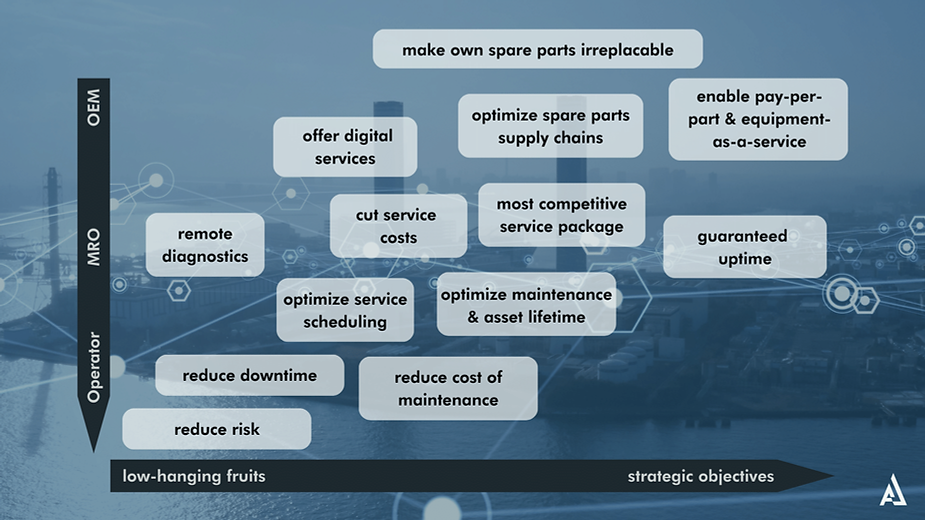
3. The Right Time to Start
Rushing into predictive analytics projects without thorough planning can result in projects ending up in a state of "Proof of Concept Purgatory." To avoid this pitfall, ensure that AI and predictive maintenance are seamlessly integrated into your overall digital strategy from the project's inception. Preliminary steps on your digitalization roadmap should include setting up IoT connectivity and creating dashboards that display performance indicators you aim to enhance through optimized maintenance, like Overall Equipment Efficiency (OEE). Making the impact visible to your customers from the start is crucial to make them understand the added value. Next to those preliminary steps, it's critical to consider data requirements early in the process to unlock the full potential of AI-enabled applications. In essence, it's about making predictive maintenance an integral part of your digital strategy right from the start.
4. Unrealistic Expectations
Setting unrealistic expectations, such as the need to predict failures "as far in advance as possible," can lead to disappointment and frustration. To avoid this pitfall, start with a clear understanding of critical components, potential failure modes, detection mechanisms, consequences of failure, and existing solutions. While qualitative insights are valuable, data-driven decision-making adds precision to your strategy. Ensure that your expectations are realistic and grounded in a thorough understanding of your machinery and its potential issues.
5. Under the Wrong Umbrella
Collaboration can be a stumbling block in predictive maintenance projects. To overcome this pitfall, ensure that your cross-functional teams work together effectively. Harmonize knowledge-based and data-driven methods, secure leadership support, and establish clear goals for a seamless, effective predictive maintenance program. Collaboration is the key to ensuring that everyone is on the same page and working towards the same objectives.By gaining a comprehensive understanding of these common pitfalls and following the practical guidance provided, machine manufacturers can navigate their predictive maintenance projects towards success. By focusing on aligning maintenance strategies with specific machinery requirements, defining clear business cases, integrating predictive maintenance strategically, managing expectations realistically, and promoting effective cross-sectional collaboration, you can optimize the implementation of predictive maintenance and set your services apart in a competitive industry.