The first AI project I got paid for involved some complex high-end machinery with data from multiple machines, each with hundreds of sensors and multiple years of operation. The challenge? Detect problems minutes, days, or even weeks before they could impact operations.
I was reading a lot of papers on deep learning innovations - particularly with time-series data, the type of data you most frequently work with in our field. But here's the kicker: it just wasn’t coming together. That's when it hit me. I'm a trained engineer. I know how this system works.
Why should AI learn, what I already know?
Monitoring an asset's condition or a manufacturing process is not an average AI project. Blindly relying on AI alone neglects decades of established best practices in condition monitoring and fails to make use of available process expertise. Not leveraging AI is like fishing without a net. Let's look at both sides of the coin.
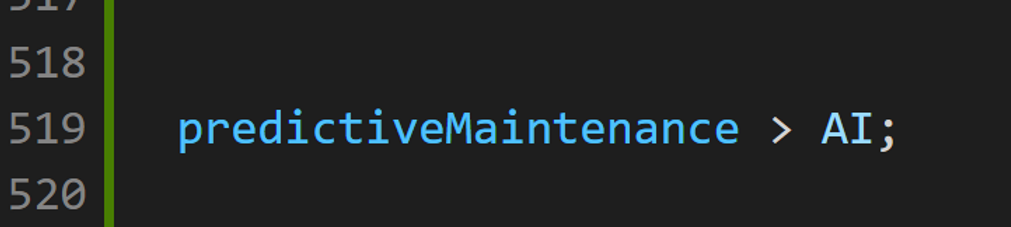
The Power of AI in Predictive Maintenance
- Automate Detection: Instead of hours spent manually analyzing data to assemble and threshold a fail-safe health indicator (which likely does not exist), self-optimizing algorithms can swiftly adjust to changing conditions, reducing the need for constant manual intervention.
Example: Consider an industrial conveyor belt system. Over time, wear and tear can cause slight variations in speed. While a human may miss this minute change, an AI algorithm can detect it, signaling potential upcoming maintenance needs.
- Reveal Unknown Cases: No expert, regardless of their experience, can predict every possible failure mode of a complex system. AI, with its vast computational capacity, can highlight anomalies that might otherwise go unnoticed.
Example: In the aerospace industry, jet engines undergo rigorous testing. But real-world conditions, like varied atmospheric pressures and temperatures, can present unforeseen challenges. AI can help pinpoint these unexpected anomalies.
- Discover Complex Patterns: Multisensor systems produce massive datasets. AI excels at sifting through this data, identifying intricate, time-related patterns that might be indiscernible to the human eye.
Example: In a vertical farm, irrigation systems equipped with sensors can detect soil moisture levels, chemical compositions, and plant health. AI can analyze this data, predicting optimal watering and fertilization schedules, and ensuring crop health.
- Provide Sensor Importance Feedback & Confidence: Not all sensors are created equal. AI can determine which sensors provide the most critical data for a given situation, optimizing the system's efficiency.
Example: In a water purification plant, sensors measure pH levels, turbidity, flow rate, and more. As an engineer focusing on contaminants, you need to know which sensors are most telling. Using AI, you quickly find out that while pH and chemical sensors give some clues, the turbidity sensor is the real star, offering the most accurate info on contamination. This insight lets you zero in on what truly matters for maintaining water quality.
- Adapt Solutions: One of the strengths of AI is its adaptability. Machine learning models can be re-fitted to cater to the unique conditions and requirements of a specific application.
Example: In renewable energy, wind turbines face different challenges based on their location — a coastal turbine encounters different environmental stresses than one in a desert. Conditions that are normal at one site may be highly anomalous at the other. AI can adjust its algorithms based on these unique conditions.
Mixing the Old with the New
The real magic happens when we blend what we've known for ages with what AI can do. How do you do that? Here's some inspiration:
- Failure Modes and Effects Analysis (FMEA): Identifies potential failure modes of a product or process and prioritizes them based on their impact and frequency. AI can automate the process of collecting data on failure modes, analyze vast data sets for patterns, and update the FMEA in real-time.
- Fault Tree Analysis (FTA): Uses tree structures to analyze the various ways a system can fail. AI can dynamically update the fault tree as new failure modes emerge, offering real-time risk assessment.
- Root Cause Analysis (RCA): Determines the underlying cause of a failure. Algorithms can sift through vast data sets, detecting anomalies and patterns that might hint at root causes faster than traditional methods.
- Life Data Analysis: Uses historical failure data to predict future failure rates. AI can constantly adjust and update models as new data comes in, offering more accurate and timely predictions.
- Virtual Sensors: In the world of data science, this concept is often referred to as "feature engineering." It's about molding raw data into highly relevant data points that bring insights to the forefront. These can be auto-generated using algorithms or crafted based on deep-rooted process expertise. Think of these virtual sensors as digital mirrors of physical sensors, each capturing meaningful information. For instance, in a compressor, raw data from inlet/outlet temperatures, pressure levels and motor current can be used to compute efficiency, specific power consumption, and heat ratios of the system. All of the prior are meaningful indicators of the system's condition and can enhance both performance and generalization of any algorithm using the data.
It's all about harmonizing established process expertise with the powerful data-driven tools we have in our portfolio today. This core concept drives innovation at Alpamayo. We take trusty methods, add a sprinkle of modern tech, and come up with ways to keep machines running smoothly.